Straight seam welding machine and circular seam welding machine are widely used in thin plate welding of oil drums, cans, radiators, aircraft and automobile fuel tanks, as well as airtight containers in jet engines, rockets and missiles.
The working principle of straight seam welding machine and circular seam welding machine:
Seam welding joint formation process (intermittent) seam welding, each welding point also goes through three stages of pre-compression, electric heating and cooling crystallization. However, due to the rapid change of the relative position between the roller electrode and the weldment during seam welding, the three stages are not as obvious as those distinguished during spot welding. It can be considered that:
1) Under the direct pressure of the roller electrodes, the metal being heated by electricity is in the “electric heating stage”.
2) The adjacent metal that is about to enter under the roller electrode is in the “pre-compression stage” by a certain amount of preheating and partial pressure of the roller electrode.
3) The adjacent metal that has just come out from under the roller electrode starts to cool on the one hand, and at the same time is under the partial pressure of the roller electrode, and is in the “cooling and crystallization stage”. Therefore, the welding zone under the roller electrode and the metal materials on both sides adjacent to it will be in different stages at the same time. For any solder spot on the weld, the process of passing under the roller is to go through the three-stage process of “preloading-electric heating-cooling and crystallization”. Since the process is carried out under dynamic conditions, the pressure effect during the pre-compression and cooling crystallization stages is not sufficient, so the quality of seam welded joints should generally be worse than that of spot welding, and defects such as cracks and shrinkage cavities are prone to occur.
Features of straight seam welding machine and circular seam welding machine:
1) Seam welding, like spot welding, is a welding process of combined thermal-mechanical (force) action. In comparison, its mechanical (force) effect is insufficient in the welding process (except step seam welding), and the faster the welding speed, the more obvious it is.
2) The seam welding seam is composed of welding spots overlapping each other, so the shunt during welding is much more serious than that of spot welding, which brings difficulties to the welding of thick plates of high-conductivity aluminum alloys and magnesium alloys.
3) The surface of the roller electrode is prone to sticking and damage, which will deteriorate the quality of the weld surface, so the dressing of the electrode is a particularly noteworthy issue.
4) Since the cross-sectional area of the seam weld is usually more than twice the longitudinal load area of the base metal (the thinner the plate, the greater the ratio), the damage must occur in the heat-affected zone of the base metal. Therefore, the seam welded structure seldom emphasizes the strength of the joint, and mainly requires it to have good sealing and corrosion resistance.
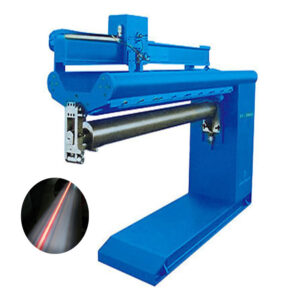
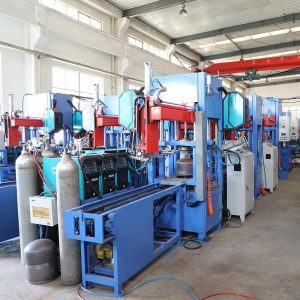
Related Posts:
- Advantages of Fire Extinguisher Circumferential…
- Steel Drum Welding Machines – The Perfect Solution…
- Classification and Development History of Drum…
- A Historical Review of the Development of Welding…
- Operation and Mechanism of Fire Extinguisher Welding…
- The Application of Welding Machines in Air Compressor Tanks